Korrosion: Entstehung und Typen von Korrosion
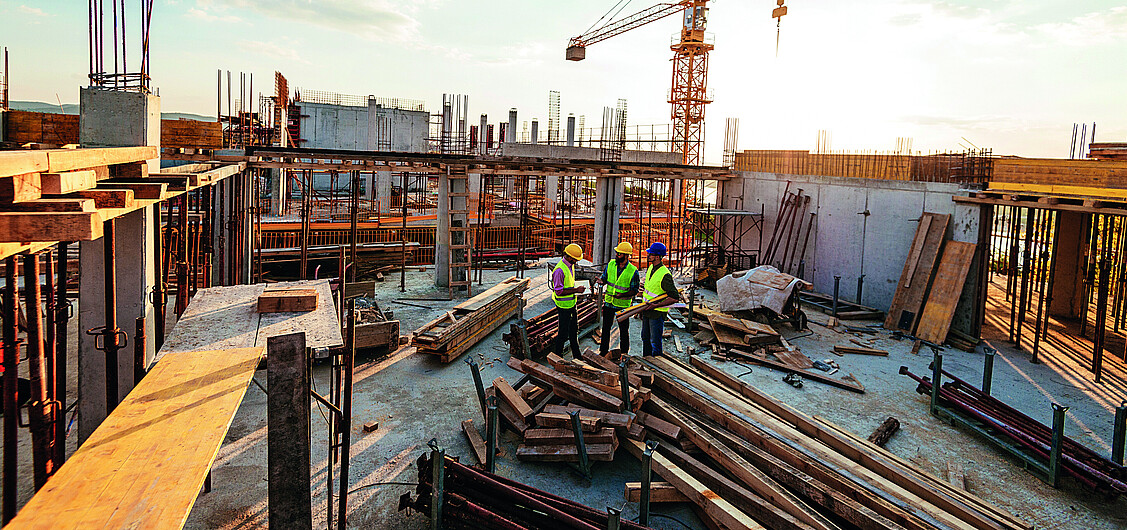
Passende Arbeitshilfen
Experten gehen davon aus, dass Korrosion bei Unternehmen, der öffentlichen Hand und Privathaushalten in Industrieländern Kosten in Höhe von 3 bis 4 % des Bruttoinlandsprodukts verursacht. Die Korrosion bewirkt zum Beispiel, dass eine Pipeline undicht wird und Öl ausfliesst. Zu beklagen ist dann ein wirtschaftlicher, aber auch ökologischer Schaden. Die Korrosion verursacht neben diesen Schäden häufig hohe Reparatur- und Wartungskosten.
Ist eine Leitung nicht einwandfrei, versickert Trinkwasser im Grundwasser. Ressourcen werden verknappt. Durch Korrosion könnten beim Wasser ausserdem die Parameter für Schwermetalle zum Nachteil der Gesundheit überschritten werden – Gefahren drohen insbesondere durch Kupfer, Blei, Nickel und auch Arsen. Ein starker Befall mit Korrosion stellt schliesslich die Sicherheit infrage: Hat sie beispielsweise tragende Teile einer Brücke massiv in einem Ausmass angegriffen, dass diese einzustürzen droht?
Korrosionsschutz ist keine Nebensache
Korrosionsschutz ist also bei Fertigung, Verarbeitung, Instandhaltung und Anwendung keine Nebensache. Ist der Schutz erfolgreich, ist er pures Geld wert und schützt Mensch sowie Umwelt. Das Fraunhofer-Institut für Fertigungstechnik und Angewandte Materialforschung IFAM geht davon aus, dass mit dem Wissen, das bereits vorhanden ist, rund die Hälfte der Korrosionskosten vermieden werden könnte. Allerdings darf nicht darüber hinweggesehen werden, dass Korrosion unvermeidbar ist. Schäden können nur mit den geeigneten Schutzmassnahmen minimiert und die Lebensdauer eines Bauteils zum Beispiel kann wesentlich verlängert werden. Aber wie sieht ein effektiver Korrosionsschutz aus, welche schweisstechnischen Anforderungen stellt er, worauf ist bei der Nachbearbeitung zu beachten? Es gilt, den ungewünschten Naturprozess zu bremsen.
Begriff und Entstehung der Korrosion
Reaktion eines metallischen Werkstoffs mit seiner Umgebung
Bei Korrosion handelt es sich aus technischer Sicht um eine Reaktion eines metallischen Werkstoffs mit seiner Umgebung. Sie führt – laut Definition nach DIN EN ISO 8044, ehemals DIN 50900-1 – zu einer messbaren Veränderung des Werkstoffs und zu einer Beeinträchtigung der Funktion des Bauteils oder gar ganzen Systems. In der Chemie ist Korrosion die chemische Reaktion oder eine elektrochemische Reaktion eines Werkstoffs mit Stoffen aus seiner Umgebung, wobei eine messbare Veränderung am Werkstoff eintritt. Allgemeiner ausgedrückt bezeichnet Korrosion die allmähliche Zerstörung eines Stoffs durch Einwirkungen anderer Stoffe aus seiner Umgebung.
Art der Belastung
Das angreifende Medium wird als korrosives Mittel beschrieben. Das können feste, flüssige oder gasförmige Stoffe sein, die das Metall umgeben und schliesslich die Korrosion verursachen. Zur Korrosion kann es also durch unterschiedliche Reaktionen kommen. Im Wesentlichen wird zwischen chemischer, elektrochemischer und metallphysikalischer Korrosion unterschieden.
Überwiegend aufgrund atmosphärischer Umgebungsbedingungen sind Stahlbauteile einer Korrosionsgefahr ausgesetzt. Art und Grösse der Belastung hängen von der Befeuchtungsdauer der Oberflächen und vom Grad der Verunreinigung der Luft ab. Ist keine Feuchtigkeit in der Umgebung des Werkstoffs gegeben, dann ist die Geschwindigkeit, mit der die Korrosion bei Eisen und Zink voranschreitet, sehr gering. Das ist auch der Fall, wenn gasförmige oder feste Verunreinigungen vorhanden sind. Wird bei einem Korrosionsangriff die Funktionalität eines Bauteils beeinträchtigt, liegt ein Korrosionsschaden vor.
Korrosion bei Stahlsorten
Un- und niedrig legierte Stähle sind durch eine ganzflächige Korrosion gefährdet. Nicht rostende Stähle und Legierungen leiden dagegen eher an selektiver oder örtlicher Korrosion. Der überwiegende Teil der Oberfläche bleibt unbeschädigt. Es treten bei nicht rostendem Stahl nur vereinzelte Korrosionsstellen auf.
Passende Produkt-Empfehlungen
Korrosivitätskategorien
Die Stärke der Korrosion kann bekanntlich stark variieren. In manchen Bereichen findet sie nur wenig „Nährboden“, in anderen greift sie umso schneller um sich. Erfasst wird sie in Korrosivitätskategorien nach DIN EN ISO 12944-2. Die Kategorien mit der Kennung C beziehen sich auf atmosphärische Umgebungsbedingungen – sie reichen von C1 bis C5. Die Einteilung in Im – von Im1 bis Im3 – legt Bedingungen im Erdreich und Wasser zugrunde. Korrosion in der Kategorie C1 gilt als unbedeutend. Sie trifft vor allem auf Innenbereiche zu. Dazu gehören beheizte Gebäuderäume wie etwa Büros. Eine geringe Stärke liegt bei C2 vor. Hier herrscht eine Atmosphäre mit geringer Verunreinigung und trockenem Klima vor, also in ländlichen Gegenden. Ein weiteres Beispiel sind ungeheizte Räume, in denen sich Kondenswasser bildet – vorzufinden in Sport- und Lagerhallen.
Hohe Feuchtigkeit
„Mässig“ kann es zu Korrosion in der Kategorie C3 kommen. Nährboden hierfür gibt es in der Stadt- und Industrieatmosphäre sowie im Küstenbereich mit geringer Salzbelastung. Das trifft auch zu bei Verunreinigungen durch Schwefeldioxid (SO2). Besitzen Produktionsräume eine hohe Feuchtigkeit sowie eine verunreinigte Luft, könnte C3 vorliegen. Vorzufinden ist diese Kategorie etwa bei Brauereien und Wäschereien. Industrielle Bereiche in Küstengegenden mit mässiger Salzbelastung, Chemieanlagen und beispielsweise Schwimmbäder begünstigen die Kategorie C4, die für eine starke Korrosion steht. Mit C5-I (Industrie), also sehr starker Korrosion, muss vor allem in Industriebereichen mit hoher Feuchtigkeit und aggressiver Atmosphäre gerechnet werden. Küsten- und Offshore-Bereiche mit hoher Salzbelastung werden mit C5-M (Meer, sehr stark) eingestuft. Im Süsswasser herrscht die Korrosivitätskategorie Im1 vor. Bauwerke und Anlagen an Flüssen sind ihr ausgesetzt. Sie gilt zum Beispiel für Wehre, Stauanlagen und Wasserkraftwerke.
Kategorien als Orientierung
Mit Im2 werden Bedingungen im Meer- oder Brackwasser kategorisiert. Vorzufinden sind sie in Hafen- und Schleusenbereichen, Molen und Offshore-Anlagen. Im Erdreich liegt die Korrosivitätskategorie Im3 vor. Mit ihr muss bei unterirdisch verlegten Rohren, Behältern und Tanks sowie Spundwänden und unterirdischen Sockeln gerechnet werden.
Tipp: Um auf die drohende Gefahr eines Schadens durch Korrosion vorbereitet zu sein, bilden die Kategorien eine wichtige Orientierung. Hersteller, Verarbeiter bzw. Schweisser sowie Anwender müssen sich entsprechend auf sie einstellen.
Rostgrade
Rost ist – in der Regel – nicht zu übersehen. Dementsprechend kann der Rostbefall auch optisch ermittelt werden. Rostgrade zeigen an, wie weit die Fläche befallen ist. Der Rostgrad an beschichteten Stahlflächen wird nach DIN EN ISO 4628-3 eingestuft. Bei Ri 0 liegt eine rostfreie Fläche vor. Bis zu rund 1 % rostbedeckt ist eine Fläche bei Ri 1, bis ca. 3 % bei Ri 2, bis etwa 10 % bei Ri 3, bis zu rund 30 % bei Ri 4 und ca. 50 % und mehr rostbedeckt ist eine Fläche bei Ri 5. Für unbeschichtete Stahlflächen werden anderslautende Kennungen verwendet – eingestuft nach DIN EN ISO 12944-4. Ist eine Stahlfläche mit fest anhaftendem Zunder bedeckt, in der Hauptsache aber frei von Rost, erhält sie den Rostgrad A. Als B wird eine Stahloberfläche mit beginnender Zunderabblätterung und beginnendem Rostangriff eingestuft. Der Grad C ist für eine Stahloberfläche bestimmt, von der der Zunder weggerostet ist oder sich abschaben lässt – es gibt nur wenige sichtbare Rostnarben. Der Rostgrad D trifft zu, wenn der Zunder der Stahloberfläche weggerostet ist und gleichzeitig zahlreiche sichtbare Rostnarben vorliegen.
Korrosionsarten
Laut DIN EN ISO 8044 gibt es 37 verschiedene Korrosionsarten. Mit Blick darauf, wo sie auftreten, werden im technischen Bereich vor allem diese Arten der Korrosion unterschieden: Kontaktkorrosion, Lochfrasskorrosion, Muldenkorrosion, Flächenkorrosion, Spannungsrisskorrosion, Schwingungsrisskorrosion, Spaltkorrosion, interkristalline Korrosion, Messerlinienkorrosion, Erosionskorrosion und Unterwanderungskorrosion.
Lochfrasskorrosion
Lochfrasskorrosion, auch Pitting genannt, entsteht auf der offenen Fläche, zum Beispiel durch Regen. Sie ist örtlich begrenzt – dabei ist sie tiefer, als ihr Durchmesser weit ist. Zu finden ist die Lochfrasskorrosion beispielsweise an Wasserrohren oder Heizöltanks aus Stahl. Lochfrass wird verursacht durch Chloride. Er ist die am häufigsten vorkommende Korrosionsart. Der Lochfrass zeigt sich zunächst als nadelstichartiger Angriff. Dabei entwickelt sich eine leicht rotbräunliche Verfärbung der Oberfläche. Nur in sehr schwerwiegenden Fällen können Anzahl und Tiefe der Löcher in dem Mass zunehmen, dass die Oberfläche gleichmässig und nicht nur nadelstichartig angegriffen wird.
Achtung: Die Gefahr der Lochkorrosion nimmt durch Fremdrost und Anlauffarben auf der Oberfläche zu. Auch Schweissschlackenreste bilden einen „Nährboden“ für diese Korrosion. Diese Schlackenreste sind beim Schweissen also unbedingt zu vermeiden.
Flächenkorrosion
Auch die Flächenkorrosion entsteht auf der offenen Fläche, zum Beispiel durch Regen. Sehr häufig kommt in der Praxis die Flächenkorrosion vor, die sich parallel zur Oberfläche des Werkstoffs bildet. Die Gefahr dieser Korrosion ist etwa an Konstruktionen aus Stahl ohne Beschichtung gegeben.
Spaltkorrosion
Eine Spaltrisskorrosion ist die Folge von eindringendem Wasser in Öffnungen. Durch die blosse Verbindung zweier unterschiedlicher Metalle kann es zu einer Kontaktkorrosion kommen, wenn der Luftzutritt in dem Spalt behindert wird. Die Gefahr einer Spaltkorrosion ist grösser als die von Lochfrass, denn sie entsteht bereits bei geringerer Belastung. Zu vermeiden ist sie in chloridhaltigen Medien durch konstruktive Massnahmen. Das gilt vor allem auch für Bereiche, bei denen sich Feuchtigkeit ansammeln kann. Falls das nicht möglich ist, ist auf einen Stahl mit höherer Korrosionsbeständigkeit zurückzugreifen. Spaltkorrosion kann grundsätzlich konstruktiv oder aber betriebsbedingt sein, also beispielsweise durch die Bildung von Ablagerungen. Einfluss auf den Spalt haben die spaltbildenden Materialarten und außerdem die Spaltgeometrie. Zu vermeiden sind enge Spalten.
Spannungsrisskorrosion
Unter Spannungsrisskorrosion ist die Rissbildung in Werkstoffen unter dem gleichzeitigen Einfluss von rein statischer Zugspannung oder überlagerter niederfrequenter Zugschwellspannung und eines spezifischen Angriffsmittels zu verstehen. Hinzu kommt die Eigenspannung. Treten Risse in Verbindung mit Schwingungen auf, ist die Rede von Spannungsrisskorrosion. Bei der Spannungsrisskorrosion treten im Allgemeinen keine sichtbaren Korrosionsprodukte auf. Die Trennung ist verformungsarm.
Interkristalline Korrosion
Die interkristalline Korrosion entwickelt sich insbesondere, wenn Chromkarbide durch Wärme in zusammenhängender kritischer Form an den Korngrenzen austreten. Werden Chromkarbide ausgeschieden, bewirkt dies eine Verarmung des Elements Chrom. Damit verringert sich der Anteil des für die Korrosionsbeständigkeit wichtigen Chroms. Zu einer solchen Wärmeeinwirkung kommt es etwa durch das Schweissen in der Nähe der Schweissnaht, also in der Wärmeeinflusszone. Allerdings tritt interkristalline Korrosion mittlerweile immer weniger auf, da immer häufiger von vornherein ein geeigneter Werkstoff gewählt wird.